沸腾燃烧锅炉基本上能烧其他类型锅炉难以燃烧的燃料,如发热量在8374千焦/千克(kJ/kg)以下的煤矸石和油页岩,也能正常的燃烧。沸腾炉每平方米火床面积能产生2.8—3.3吨/时(t/h)蒸汽,是层燃炉产汽量的2~4倍。
沸腾锅炉,如能配备上灰渣利用装置,就能构成一种比较完善的燃烧劣质燃料的综合利用系统。我国劣质煤资源十分丰富,劣质燃料的开发和利用,对合理地使用我国能源资源具有相当重大的意义。因此,沸腾炉在我国有着广阔的发展前途。
一、沸腾炉结构形式
沸腾炉有全沸腾炉和半沸腾炉两种形式。这两种沸腾炉在结构原理上有所不同,在工作性能上也有一些差别。
1.全沸腾炉 在全沸腾炉中,燃料颗粒完全被气流所“流化”,作着类似于液体沸腾样的“流动”。燃料就是在这样剧烈的、杂乱无章的“沸腾”运动状态下进行燃烧。同时,在这种沸腾燃烧层中,一般都埋设有一定数量的管子受热面,称为“埋管”受热面。这种受热面可以获得强烈的沸腾层的传热。
图3—27是全沸腾炉的结构原理图。空气经进风管被送进风室后,在布风板的分配下均匀地进入炉子的下半部——沸腾段。气体在沸腾段中向上流动,直至流出沸腾段,流遍整个炉膛。燃料是从进料口被送入沸腾段的。由于沸腾炉一般燃用粒径为0~8毫米(mm)以下的煤末,燃料的颗粒直径的范围较宽,因此,在燃料进入沸腾段以后,一部分细粉[颗粒直径在2毫米(mm)以下者]被气流吹出沸腾段,进入沸腾段上面的悬浮段,并在那里进行悬浮燃烧。其余绝大部分燃料颗粒则留在沸腾段内,在沸腾运动过程中完成燃烧。燃尽的灰渣从溢流口溢出。由于全沸腾炉一般都采用溢流除渣,故又称为溢流式沸腾炉。
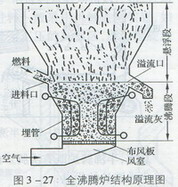
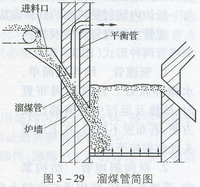
综上所述,沸腾燃烧、沸腾层传热和溢流除渣是全沸腾炉最基本的特点。
2.半沸腾炉如图3—28所示,其结构特点是下部装有一副很窄的链条炉排,起着进料、布风和出灰渣的作用。炉排是倾斜布置的,倾角一般为10°~18°,倾斜的目的在于造成一个“沸腾池”。炉排尾部高出沸腾池,形成层燃段。半沸腾炉主要是因此而得名。半沸腾炉的链条炉排结构与普通链条炉排大致相同。炉排下采用分段送风,以便使各风室的风压与那里的燃料层高度适应。炉排前部为沸腾床,需要较高的风压;炉排后部基本上是灰渣的层燃燃尽段,只需要很低的风压。一般风室风压自前至后为2000~500帕(Pa)。在沸腾池以上宜布置二次风,以求加强空间的扰动,延长飞灰在炉内的停留时间,由于半沸腾炉的沸腾层高度较小,一般只有600毫米(mm)左右[全沸腾炉中可高达1—1.4米(m)以上],因此,不能布置埋管受热面。
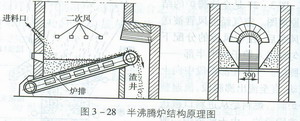
总之,半沸腾炉既有沸腾炉的性质,又有层燃炉的特点。
半沸腾炉的优点:
(1)半沸腾炉具有比链条炉高得多的热强度。它的炉排面积热负荷比普通链条炉高出10倍左右。
(2)半沸腾炉的送风压力比全沸腾炉低,一般仅为1500~2000帕(Pa),与普通链条炉排相近,因此,运行电耗较低。半沸腾炉对结渣并不十分敏感,燃烧温度可允许高些,而全沸腾炉的沸腾层温度一般须控制在1000℃以下。
半沸腾炉虽然具有层燃炉的某些优点,但也不能充分发挥沸腾炉的优越性。由于半沸腾炉是采用链条炉排,其结构比较复杂,制造工作量比较大,金属消耗量也较多,运动着的炉排工作可靠性较差,密封不好,极易漏风。因此,在需要最大限度地发挥沸腾燃烧优越性的情况下,半沸腾炉显然不如全沸腾炉优越。在我国工业锅炉中,采用沸腾燃烧的锅炉,几乎都是全沸腾炉。
二、进料方式
根据炉膛中进料口所处部位的不同,进料方式分为正压进料和负压进料两种。进料口设在正压区(溢流口以下)者,称为正压进料;进料口设在负压区(溢流口以上)者,称为负压进料。
正压进料时,全部燃料经过高温沸腾层,有利于细粒燃料燃尽,因而可以降低飞灰带走的损失。但进料口必须密封严密,且新燃料在进料口处容易堆积。正压进料一般采用机械进料装置,如采用螺旋给煤机等。由于进料口处于正压的高温区,所以螺旋给煤机的工作条件较差。
为了简化进料机构,并提高其工作可靠性,目前采用溜煤管(图3—29)来代替螺旋给煤机。溜煤管以50°以上的倾角斜插入炉内正压区,管内燃料依靠煤柱压力直接注入炉内。为了防止从进料口喷火、冒烟,在炉墙内装设平衡管,使溜煤管与炉膛负压区连通。煤封良好时也可不装平衡管。
负压进料与正压进料相反,由于燃料从沸腾层以上进入,因此,有部分细粒燃料未经沸腾层就被上升烟气流带走,增大了飞灰热损失。在负压区的进煤进料装置比较简单、可靠,而且系自由落下,故播散度大,不易造成料口堆料。
三、埋管
埋设在沸腾段内的受热面管称为埋管。埋管受热面具有很高的传热系数,因而可以大大节省受热面的金属耗量。同时,埋管能保持沸腾层温度,可有效地防止高温结焦。
沸腾段内的结焦问题是影响沸腾炉安全运行的一大障碍。产生结焦的直接原因是沸腾段料层温度过高。为了避免沸腾段内的结焦,必须合理地布置埋管受热面,在运行中须正确地调节风量与煤量。
在锅炉出力一定的情况下,埋管受热面的多少取决于燃用的煤种。对于现已生产的或经过改装的沸腾燃烧锅炉来说,每生产1吨/时(t/h)蒸汽,所需埋管受热面约为1.3~1.5米2(m2)。埋管受热面是按实际埋入沸腾层中的管子外表面积计算的,这一点与一般炉内辐射受热面的计算方法不同。
埋管主要有竖埋管及横向斜埋管两种形式(图3—30)。
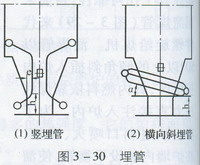
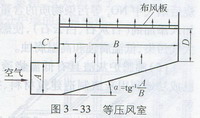
1.竖埋管结构较简单,水循环较好。若靠四周布置时,检修及运行中打渣都比较方便;若布置不好时,在下部弯头处磨损较严重。
2.横向斜埋管 结构紧凑,受热条件好,特别适宜在较大容量的锅炉中使用。其缺点,是当管子紧密布置时,检修及运行中打渣都不方便,而且整个管子还会遭受定向磨损,受磨损的范围较大。
埋管受热面的主要缺点是受到燃料颗粒的剧烈磨损。目前比较有效的防磨方法是在管子易磨部位加焊防磨圆钢。防磨圆钢的布置方式也是因地而异的,有的沿管子径向焊圆钉(抓钉),有的则沿管子环向焊孤条(月牙条),也有的沿管子轴向焊棒条(图3一31)。
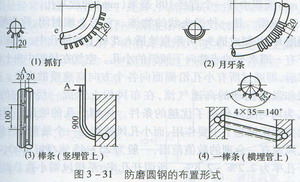
埋管受热面的传热系数很高可达233~535瓦/米(米2·K)[W/m2·K],对沸腾层内温度的影响很大。受热面过少,会引起高温结焦;而受热面过多,则又会导致炉温过低,影响燃料的着火和燃烧。因此,埋管的受热面积必须精确选取。
四、布风装置
沸腾炉布风装置的主要作用是均匀地分配气体,使空气沿炉膛底部截面均匀地进入炉内,保证燃料颗粒流化均匀。
布风装置是沸腾炉的关键部件,沸腾炉工作的好坏,很大程度上取决于布风装置的结构。
目前在沸腾炉中应用最广是风帽式布风装置。它由花板(多孔板)、风帽和风室等组成。其中花板和风帽组成一体,称为布风板。
1.花板是由钢板或铸铁板制成的多孔平板,用它来固定风帽,并使之按一定方式排列,以求达到均匀布风。花板的尺寸应与炉膛相应部位的内截面相适应,厚度为20~35毫米(mm)左右。风帽插孔一般按等边三角形布置,孔距为风帽直径的1.3~1.7倍,帽沿间的最小间距不得小于20毫米(mm)。通常每1.3~1.5米2(m2)面积中开一个直径108毫米(mm)的放灰孔。
2.风帽是一种弹头状的物体。它的上端封闭,称为帽头,下端敞开,并制成插头,可垂直地插入花板上的插孔中。风帽的颈部开有一圈水平的或略向下倾斜的小孔。空气在风帽中向上流至颈部后,即通过所有小孔沿侧面向各个方向高速喷散出来。高度分散和强烈扰动的高速气流,在布风板上形成一层均匀的“气垫”,为均匀配风创造了优越的条件。风帽小孔的喷散作用对空气的分配质量起了主要作用,而小孔风速则是一个最重要的参数。小孔风速有一合理的数值范围,一般为25~45米/秒(m/s),相应的开孔率为2.2%~2.8%。所谓开孔率,系指风帽小孔总面积和布风板面积之比。
风帽有菌形(蘑菇形)、柱形、球形和伞形等形式。其中应用最广的是菌形风帽。柱形风帽是目前应用较多的一种新型的风帽。这两种风帽的结构及其固定方法,如图3—32。
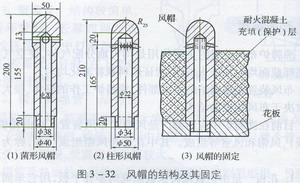
菌形风帽,风帽颈部钻有直径6~8毫米(mm)的小孔6~8个。小孔可以是水平的,也可以钻成向下倾斜15°的斜孔。这种风帽的阻力小,工作性能良好,但结构稍较复杂,清渣较为困难,在帽沿处经常出现卡渣现象。此外,风帽菌头部分冷却面不够,容易出现氧化烧穿等现象。这种风帽逐渐被柱形风帽所取代。
柱形风帽,由于取消了帽沿,因而尺寸更小,构造也更简单,并且还克服了菌形风帽的一些缺点,因此工作性能更为良好。
3.风室(风箱) 风室的结构对布风的均匀性有一定的影响。目前,风室结构已有很多种,但是结构简单,使用效果最好的却是等压风室(图3—33)。等压风室的结构特点是有一个倾斜的底面,能使风室内的静压沿深度保持不变,因而有利于提高风量分配的均匀性。
为了稳定风室气流,在斜底以上须留出一个稳定段。稳定段的高度D不宜小于500毫米(mm)。同时风室的进口风速也须加以控制,使之不超过10米/秒(m/s)。风室中水平风速要低些,一般为1~1.5米/秒(m/s)。
五、沸腾炉的优缺点
1.优点
(1)由于沸腾炉的燃料层很厚,平均温度较高(850—1050℃),燃料在炉内停留的时间长,又不断地互相碰撞,对燃料的着火条件非常有利,可以燃用品质极低劣的燃料,灰分大、水分多、挥发分少的劣质燃料也能稳定地燃烧。这是沸腾炉的最大优点。
(2)沸腾炉能强化燃烧,其燃烧热负荷和埋管传热系数都非常高,因此,可以大大地缩减炉膛尺寸,一般可比同容量的其他型锅炉缩减一半左右。这一点对于大型锅炉是特别重要的,因为沸腾炉可以减小金属耗量和安装费用。
(3)沸腾炉的结构简单,机械传动装置少,容易使燃烧固体燃料的小型锅炉实现机械化和自动化。
(4)沸腾炉为低温燃烧,因而可以燃用低灰熔点的燃料。燃烧后烟气中NOx等污染物质的含量也较少,而且也易于向燃料中加入添加剂(石灰石、白云石),使燃料脱硫,从而可以进一步减少大气污染、低温腐蚀和高温腐蚀。
(5)沸腾炉灰渣具有低温烧透的性质,便于综合利用。目前已成功地利用灰渣制造建筑材料、提取化工产品,用作农田肥料等。
(6)负荷调节性能好。沸腾炉能在较低的负荷下工作。
2.缺点
(1)锅炉热效率低 一般沸腾炉效率在60%~70%之间。这主要是因为机械不完全燃烧损失q4很大所造成的。q4值与所用燃料有关,燃用石煤和煤矸石q4为20%~30%;燃用劣质烟煤为15%~20%;燃用劣质无烟煤为20%~25%;燃用褐煤为5%一15%。沸腾炉的机械不完全燃烧损失之所以大,完全是由于飞灰量大而带走的热量所造成的。因此,如何减少飞灰含碳量、提高燃烧效率是解决沸腾燃烧技术的关键。
(2)埋管磨损快 壁厚3.5毫米(mm)的埋管使用3个月到半年,即被磨穿。但若采取防磨措施,一般能运行1年左右,有的甚至能运行2年以上。
(3)耗电量大 电主要消耗于高压送风、碎煤等项工作上。沸腾炉的单位蒸发量的耗电量比一般煤粉炉高1倍左右。
(4)飞灰量大,烟气排尘量大,除尘系统的工作量大,除尘效果欠佳。
TAG: 锅炉工